Having had 30 years of personal experience in the geothermal industry in Canada, including time spent in:
|
|
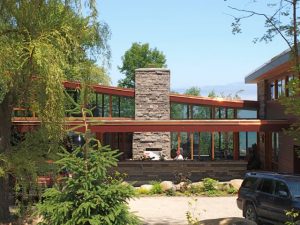
5,000 sq. ft. Home Near Collingwood, Ontario
I have personally been directly and indirectly involved with literally thousands and thousands of geothermal heat pump system installations. The picture at right shows a custom home with a geothermal system system that I designed installed and commissioned with my crew in 2008.
In 1983 when I first became involved in selling geothermal systems, the best units available were really modified commercial water source heat pumps. Although geothermal systems were the most efficient heating technology available even back then, they were crudely manufactured and much less efficient than today’s equipment.
That was a time before on-board DHW desuperheaters and DHW pumps, capacity staging high efficiency scroll compressors, ICM/ECM motors, microprocessor controls and on-board diagnostics came to geothermal heat pumps. At that time, most installers new little about designing earth loops in a manner that would provide a low pressure drop and low pumping kW. penalty while maintaining turbulent flow inside the loop and thus, more efficient heat transfer. Or for that matter what antifreeze fluids could provide adequate heat transfer to the system, remain at a sufficiently low viscousity throughout the anticipated operating range without being corrosive to the heat pump heat exchanger and other metal parts of the system such as the loop pumps. No company built a durable pump kit/flow centre that wouldn’t sweat with condensation and rust all over back then either.
As stated above, systems were crude compared with todays systems and yet, even in those early days, the technology was quite forgiving and worked remarkably wel. Many early systems were installed in less than an optimal way and our customers were truly the pioneers in the marketplace. Those earlier times however, provided us with the experience and the knowledge of what improvements were needed. Yes those early systems have been overall, remarkably forgiving and the majority are still up and running in one way or another. Some customers have replaced worn out heat pumps over the years, connecting them onto existing earth loops that are 20+ years old, thus gaining the advantages in performance offered by todays equipment. Some have simply maintained their heat pump equipment and they are still operating the way they were originally. I have seen 30+ year old equipment still operating today however I have also seen tremendous improvements in many areas of geothermal equipment design – including but not limited to:
|
|
More manufacturers today supply their contractors with system design software than ever before. Softawre helps the installer size the heat pump and the earth loop with accuracy and can also provids an energy use comparison between a geothermal system and fossil fuel or all electric system.
New system purchasers today are fortunate to have by-passed the industry’s learning curves for the most part. Some manufacturers are training dealers by the score in sizing and installation techniques. Once relagated to a fringe technology, more of the large, well established HVAC installation companies have added geothermal systems to their product line up, illustrating a more mainstream acceptance of geothermal technology.
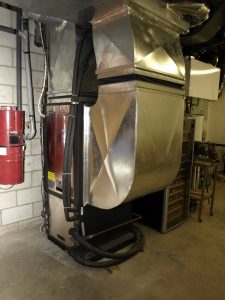
Modern Ducted Water to Air System
Industry Shortcomings:
As great as the new equipment and sales and installation training are however, in my experience the industry has performed nowhere near as well when it comes to training contractors in geothermal specific, service and preventative maintenance. There has been an expectation that this aspect of the business would be brought to the table by sevice technicians existing skill set.
What has been overlooked is the fact that most of our industry’s trained HVAC technicians are gas fitters and/or air conditioning technicians, not heat pump trained people. Add to that fact that over the years, just to stay in busines the heat pump distributors have built their businesses by selling equipment to just about any trades company that was interested in selling equipment, i.e., plumbers, electricians, insulators, sheet metal mechanics, water softener installers, solar installers, etc.,and not necessarily HVAC firms. Distribution of heat pumps, quite out of necessity, has been to contractors in almost any trade remotely related to water, electricity, air and heat and they were trained primarily is sales and installation and not in service and maintenance.
Far fewer technicians who install geothermal are also refrigeration mechanics for example. That statement doesn’t mean that a refrigeration mechanic is the only trade that can service heat pumps, but the difference in knowledge and skills acquired between an a/c tech and a refrigeration mechanic are huge. Some of the most knowledgeable refrigeration mechanics are those involved in fitting grocery store systems or those involved in industrial process cooling. Such mechanics are familiar with complex refrigeration systems and are more likely to understand the more complex multi-function heat pumps now on the market.
As there has been little training in servicing and preventative maintainence of even the simpler systems it is important that the consumer understands that their “top of the line” heating and cooling system is not mainenance free. So many many geothermal systems are installed and left to run without maintenance for years. Eventually something critical to system operation breaks down and an expensive repair is needed. Often, regular preventative maintenance can prevent those costly repairs.
They Died Too Young:
Recently I came accross two 8 year old geothermal heat pump systems that were installed on the same estate. They were replaced with new heat pumps of a different brand because the mechanic could not find a refrigerant leak on one unit and because the second unit had repeated blower motor problems.
I know from experience that some small leaks can be very difficult to find, but there is a finite number of places for a leak to occur, so leaks can always be found with enough dilligence. Had I known about this situation, if we could not find the leak we would have likely recommended removing the heat pump temporarily to find the leak and repair it. To find a leak that was difficult to locate we have occassionally taken heat pumps to a shop, fround the leak and rebuilt repared them on the bench. The cost to do that in the case mentioned above would probably been about 20% of the unit replacement cost. I don’t think I would ever scrap a heat pump with at least 2/3 of its useful life still ahead of it.
The same goes for an electrical issue such as a blower motor. Motors always fail for a reason. Even a troublesome electrical system can be replaced with something better, right down to the control board replacement for much less than the cost of a replacement heat pump. I believe ythis owner was not served very well by his technician. The technician’s company did very well though by selling two brand new replacemnet heat pumps and connecting them to the existing earth loops.
The Need for Regular Heat Pump Preventative Maintenance – Reading For the Technically Inclined:
Although there has been a trend to incorporate partial home or whole home radiant floor heating into many new custom homes over the last twenty years, most geothermal systems sold in Canada today are forced air systems that provide both heating and cooling year round through a ductwork system of some type.
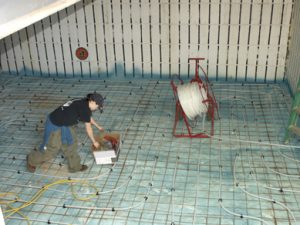
RFH Technician Laying Floor Heating Pipe
In this respect geothermal heat pumps are like any other type of regular high efficiency or regular efficiency furnace.
A fan inside the cabinet creates a suction or low pressure on the incoming (return air) side of the ductwork system and a high pressure on the leaving (supply air) side of the system.
Regardless of how clean you keep your home, dirt and dust are inevitably sucked into the cabinet by the fan. Any gaps in the sheet metal of the cabinet, e.g., around the doors and the filter rack, are easy entrances for dirt, dust and debris. To prevent long term problems from occurring therfore, like any other heating system you have ever owned, a geothermal system should be cleaned and inspected at least anually and buildings/homes that experience more severe conditions, (e.g., lots of children and pets entering and leaving, country homes, old dusty farm houses or high traffic areas, etc.,) twice a year, typically spring and fall.
Long Term Cleaning Neglect:
If a system isn’t cleaned regularly, wherever it can settle or cling, dirt, dust, dander, pet fur, bugs and you name it, build up inside the heat pump, year after year. Any dirt and grime that lands on the points of the main electrical contactor, (the high voltage, heavy duty switch that turns on the heat pump’s compressor and several other devices), carbonizes on those points, resulting in a growing potential for electrical arcing and continuous carbon build up.
The main contactor handles the full start up amperage of the entire heat pump, typically between 86 and 186 amps depending upon the unit size. As carbon builds up over time, more and more arcing occurs. Without cleaning, the point surfaces themselves become prematurely pitted and uneven.
Dirt build up, point deterioration and arcing places higher and higher stresses on the starting components which can eventually become critical even damaging the compressor motor windings themselves resulting in harder and harder starting and eventually compressor failure. When this happens, a compressor replacement is needed.
Note: Even when a heat pump sytem is serviced annualy, normal wear on the contactor points will occur. It is a pretty good rule of thumb in our experience, to simply to expect to change the main contactor out every 5 to 8 years. Replacing that $100 part every 5 to 8 years can save thousands of $$$ and a really big customer upset in the long run.
Shouldn’t a Compressor Failure Be Covered Under the Manufacturer’s Warranty?
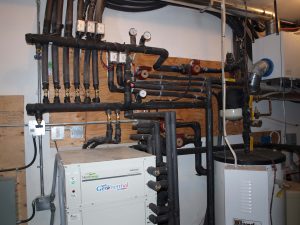
Modern Hydronic Water to Water System
The answer to the question above is maybe. All manufacturer’s warranties specifically cover defects in the material or workmanship. Compressors can breakdown for a variety of reasons but there is always a reason. Unless there is a defect in the compressor manufacture itself, there has to be another reason for the failure. Depending upon the manufacturer and contractor a replacement compressor may be supplied with no additional questions asked and the reason for the failure may never be discovered. On the other hand a heat pump manufacturer is perfectly within their rights to ask the contractor for details of the reason for the failure and if it is deemed that a compressor failed within the warranty period due to lack of maintenance, the heat pump manufacturer may deny warranty coverage.
It is important to note that the actual compressor manufacturer’s warranty to the heat pump manufacturer is typically only 6 months from the date of compressor manufacture. A compressor may sit on the heat pump manufacturer’s shelf for longer than that before being built into a heat pump. That is why compressor warranties vary cosnsiderably from manufacturer to manufacturer. A large manufacturer will likely move through compressor stock quickly and may have some recourse with the supplier and a smaller manufacturer may not. So in reality the financial burden of a 5 or 10 year parts and one year labour refrigeration circuit warranty, (including the compressor), is carried by the heat pump manufacturer and somewhat by the installing contractor who is usually credited an unrealistically low labour allowance for changing out the part.
Guess What!
Most compressors today are very well built to extremely high tolerences to meet high legislated efficiency standards, while still providing reliability and longevity.
Usually compressor failures are not due to compressor deffects and are due to some type of mechanical cause, e.g., a lubrication failure causes a seizure, constant voltage irregularities result in motor starting duress. If the reason for a compressor failure remains undiagnosed at the time of replacement and the true cause is not corrected, there is every likelyhood that the replacement compressor will fail too and in short order. The second replacement compressor will probably not be covered by warranty. So it really behooves us all, industry members and consumers alike, to determine the real reason for a compressor failure and correct that problem at the time of replacement too.
Manufacturer’s warranties are provided to specifically cover the system in case of a defect in material or workmanship. So perhaps the right question to ask at such a time is “should a compressor fail due to lack of maintenance of the heat pump, or from any other cause that is not a defect in materials or workmanship, e.g., electrical brown outs or power surges, lightning, etc., should the compressor failure be covered under warranty?”
After all, if your new car engine started burning excessive amounts of oil within the warranty period because you neverchanged the oil as recquired in the owner’s manual, would the manufacturer fix or replace the engine under warranty? Likely not, because that situation as annoying and as expensive as it would be for the car’s owner, is not truly warrantable? The automobile manufacturer would be well within their rights to ask to see the oil change receipts and deny the claim when they could not be produced.
One Further Point on the Maintenance and the Manufacturer’s Warranty?:
I have often noticed that because homeowners purchased the type of heating systems that requires the largest capital investment, they tend to expect their geothermal heat pump systems to be virtually maintenance free. That is just not so.
Although a geothermal heat pump is considered lower maintenance and even less complex in some ways than other types of high efficiency heating and cooling appliances, they are not immune to dirt and dust and wear and tear. They do need to be cleaned and maintained just like any other type of comfort system.
E.g., even though the Cadillac costs more up front than a Chevy, one changes the oil on a Cadillac and a Chevy at approximately the same interval.
What is Involved With Preventative Maintenance:
As mentioned above, usually over time a geothermal heat pump takes less maintenance than a high efficiency gas furnace does. After all, there are less redundant back up safety systems in a heat pump. Unlike with a gas system, there is no need to prevent explosions or carbon monoxide formation for example. Heat pumps need less maintenance than a high efficiency oil furnace too. According to manufacturer’s recommendations, high efficiency oil systems should be stripped down to the heat exchanger and inspected for HX perforation annually. Such annual service checks are deemed necessary because the acidic by products of oil combustion have the potential to mix with the condensed water vapour formation from a condensing furnace, which can combine to form a strong acid having a potential to rot out the oil the furnace heat exchanger, (even stainless steel), very quickly.
20 Points of Typical Geothermal System Annual Maintenance:
|
|
Typically Accessory Maintenance:
Frequently homes having a geothermal system will also have a Heat Recovery Ventilator, (HRV) and/or a high performance HEPA, Carbon or TFP air cleaner installed in conjunction. We are typically asked to include those accessories in our maintenance work as well.
Further as a good will measure really we generally inspect the client’s DHW tank for the proper temperature settings upper and lower and for pump operation and circuiting when it is connected to the geothermal system.
For answers to your Geothermal questions, e-mail info@gerryongeo.com.com or Telephone 226-377-3987